Wood’s structure and general properties
Wood is a porous three-dimensional, hydroscopic, viscoelastic, anisotropic biopolymer composite composed of a coupled matrix of cellulose, hemicelluloses and lignin with minor amounts of inorganic elements and organic extractives. Each wood species has its own set of property values that result in certain characteristics making one wood species more favourable to be used for a certain purpose than another, but there are some properties that unify all species such as the general cellular structure and growth pattern and thus form the basis for all wood properties.
Wood in the forest
Any tree, and thereby wood, grows by means of photosynthesis. In this process, CO2 is taken up into the leaves and in combination with water and powered by the light’s energy it is chemically transformed to sugars that lay the basis for the assembly of all cells. In the process, carbon is absorbed and oxygen is released back into the atmosphere as a by-product.
The wood cells originate from the cambium, the growth-zone of the tree right underneath the bark. Thus, cell layers grow concentrically around the pith in the middle of the tree. Depending on the species and the availability of resources the growth within each year can vary.
Generally, tree species are divided into softwoods and hardwoods. Softwoods include coniferous trees while hardwoods include all deciduous trees. The majority of wood used for construction purposes is from softwood species.
From an evolutionary perspective the softwood species are older and therefore have a less complex cell structure. The fibres (in softwoods called tracheids) are longer, and the wood typically grows faster, generally resulting in a lower density compared to hardwoods although there are exceptions to this rule. Softwoods are usually ready to be harvested within 50 – 80 years of age, depending on the desired purpose. A few fast-growing softwood species e.g. radiata pine can be harvested in rotations shorter than that. In contrast, hardwoods generally require longer rotations to be harvested in some cases more than a 100 years, depending on the species and geographic location.
Ideally, trees used for construction wood have a straight trunk with little to no branches in its lower half leading to a high yield of boards with a minimum of knots influencing mechanical properties. To reach this desired outcome, forests require continuous management, meaning that the correct growth of promising individuals is enabled by reduction of the trees surrounding it.
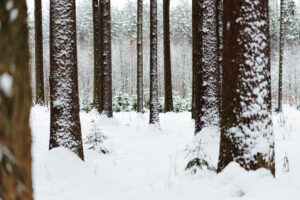
Wood on a cellular level – structure and cell types
Wood cells consist of mainly three components: cellulose, hemicellulose, and lignin. These components are incorporated into each wood cell in a specific order giving strength and stability while also maintaining flexibility. The multi-layered secondary cell wall is surrounded by a primary cell wall. The space in between the cells is filled with and thus connected by the middle lamella that acts as a glue between the cells.
The number of cell types that are present in wood depends on the general distinction of softwoods and hardwoods and can also differ in wood species.
In contrast to hardwoods, several softwood species contain resin canals. However, about 95% of cells in softwoods are longitudinal cells called trachieds, which provide the double function of water transport and structural strength in the living tree. They are longitudinally and radially interspersed with parenchyma cells that have a storage function.
In hardwoods the number of cell types with specific functions is more diverse and thus leads to a more complex composition of the wood.
A unifying characteristic for most softwood species is that in spring, when tree-growth resumes, new cells (tracheids) have rather thin cell walls and big lumen favouring water transport. Over the course of the growth period the thickness of the growing cell walls increases. This leads to the annual rings having a rather light appearance at the beginning of the growth period (earlywood) before they become darker (latewood).
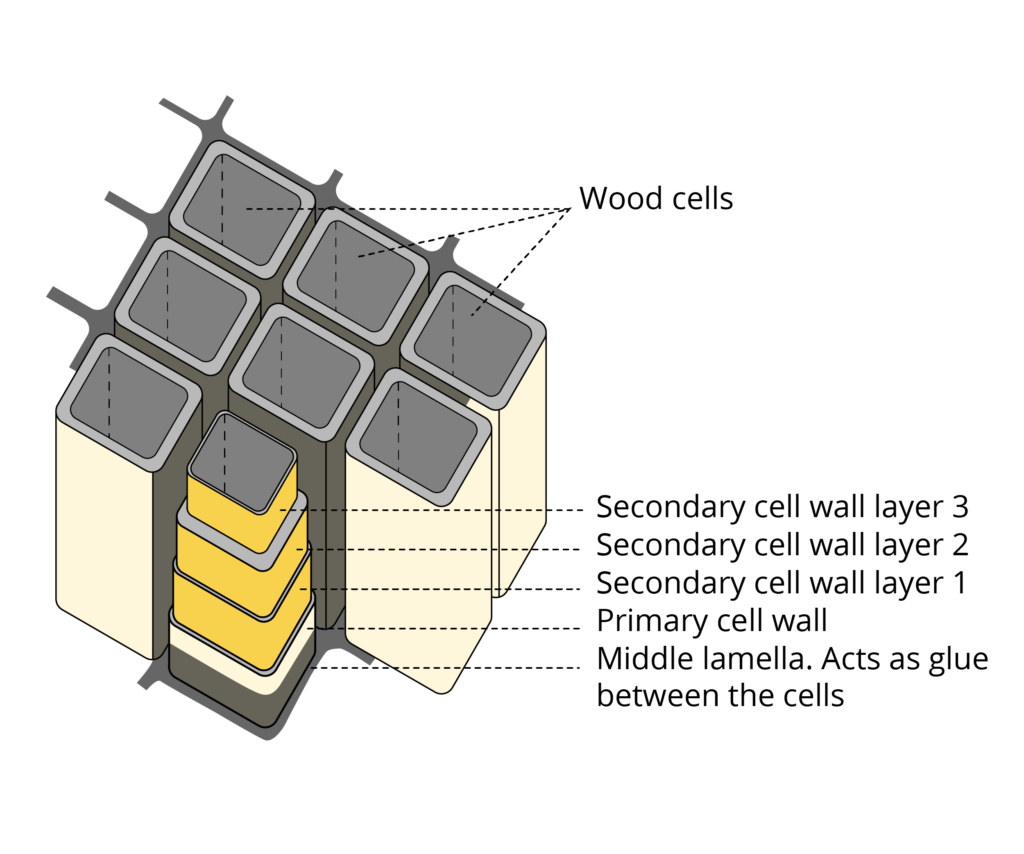
The three main directions in wood – longitudinal, radial and tangential
It is important to consider the direction in which wood is cut because it does not only change its optical appearance, but also impacts a range of wood properties due to its anisotropic behaviour. Considering i.e. bending strength, the strength value is approximately 10 times higher when force is applied perpendicular to the grain than when it is applied parallel to the grain. In contrast to this, looking at tensile strength of wood, the strength can be 10 – 20 times higher parallel to the grain than it is when applied perpendicularly.
Another area impacted considerably by the direction of wood is its shrinking and swelling properties. While shrinkage and swelling in the direction of the fibres is minimal the dimensional change in radial direction as well as in tangential direction is considerable.
The three main directions that is differentiated between in relation to a tree’s axis are longitudinal, radial and tangential. A longitudinal cut shows the cross-section of a tree trunk where all annual rings appear in a circular shape. A radial cut always goes through the centre of a tree trunk (pith), parallel to its axis, which causes the annual rings to appear in distinct lines along the cut surface. A tangential cut also runs parallel to the tree trunk’s axis, but it does not cross the pith. Thus, the annual rings will show in differently shaded and sized surface areas.
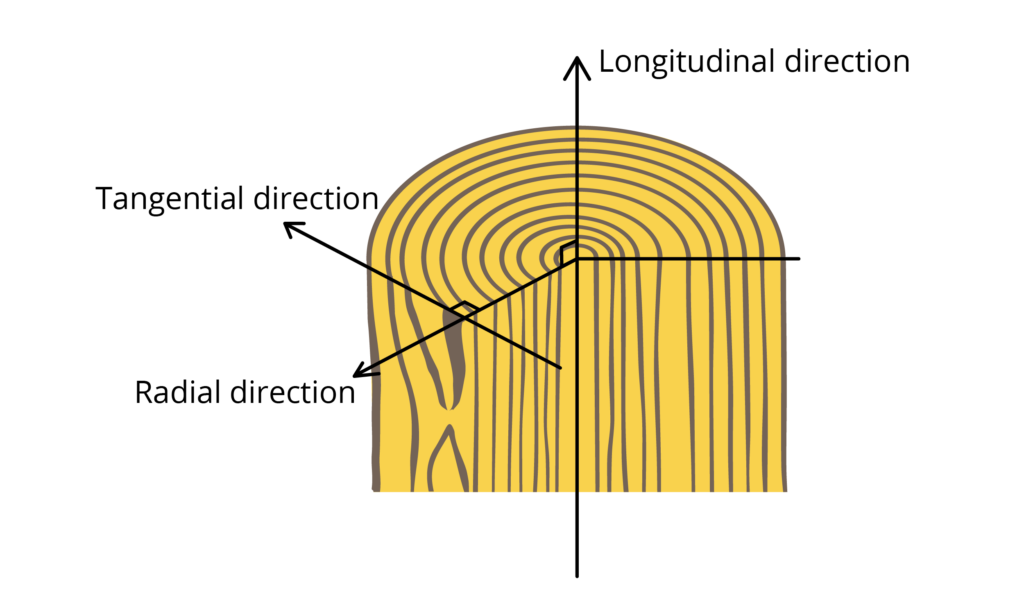
Heartwood and sapwood
Heartwood consists of dead cells and develops outwards from the centre of the tree trunk. While heartwood fulfils mechanical functions only, sapwood is the “living” part of the wood that transports water and nutrients to the assimilating parts of the tree.
The age at which heartwood formation begins varies depending on the tree species. In younger trees, the quantity of sapwood is much higher than that of heartwood and the proportion of heartwood to sapwood increases with age.
In some species, heartwood can be distinguished from sapwood by its color, with sapwood being lighter than heartwood. In some species, sapwood can have a higher permeability, making it suitable for impregnation treatments, i.e. to enhance durability. Pine sapwood is a prime example for this practice.
Heartwood is generally drier, heavier, and harder; the pores connecting wood cells are closed and stored nutrients are either removed or transformed to extractives. It is generally more dimensionally stable and is slower to dry than sapwood.
When it comes to natural durability, it is heavily dependent on the wood species whether there is a difference between heartwood and sapwood. Oak heartwood, as an example, has a high natural durability compared to sapwood while beech heartwood does not have improved durability compared to beech softwood.
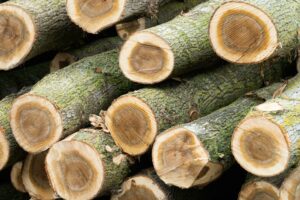
Density of Wood
Density indicates the relation of mass per volume. The density of wood varies from wood species to wood species and has an impact on other properties such as strength and swelling which increase with increasing density.
Variation spans from the lightest wood being Balsa (100 kg/m³) to the heaviest wood being Pockwood (1.200 kg/m³).
Commonly known and used wood species range in their density between 470 kg/m³ (spruce) and 780 kg/m³ (European beech) with species such as pine (490 kg/m³), fir (530 kg/m³), larch (620 kg/m³), and oak (710 kg/m³) being within this span. Each of these numbers are average values for wood conditioned at conditioned at 20°C and 65% rel. humidity, which can vary considerably within each species.
Workability
Wood can be easily cut, shaped, and joined using basic tools and common woodworking techniques. Drilling, sawing, planning, and sanding are processes that are done on an industrial level but are also possible by smaller portable / handheld units that allow on-site product adaptations if needed.
The most common softwood species used for construction (pine, spruce, and Douglas fir) are all easy to shape, nail, drill, and glue. While woodwork does require a certain degree of expertise, it does not have the need for as much specialization as working with concrete or steel does.
Mechanical properties
Mechanical properties describe a material’s “behaviour” when subjected to external forces. They indicate e.g. elasticity and stiffness and thus deformation. When using wood for construction, it can be important to define its ability to bear a load over a long period of time.
As wood is a naturally grown material it is not as homogenous as e.g., steel or concrete, and therefore can vary considerably in its properties, even within a wood species or between boards cut from the same tree. In addition, the properties are affected by the wood’s moisture content and density as well as the presence of knots etc.
Strength classes
The direction of the grain in relation to the applied force must be considered. Methods for strength grading can be either visual or they can be based on mechanical testing. Visual strength grading is not to be confused with visual appearance grading (e.g. EN1611-1 for softwoods). EN 338 defines bending strength classes for softwoods (C-grades) and for hardwoods (D-grades). These grades unite information about strength, stiffness, and density values, and form the basis for design calculations
Compression strength
Solid wood exhibits the highest compression strength in longitudinal direction. The maximum compression strength is about half of its respective tensile strength. Compression strength perpendicular to the grain is very low. This property calls for additional reinforcement in case of transverse pressure loads.
Tensile strength
The tensile strength of wood is lowest when force is applied perpendicular to the grain. In this case wood exhibits only around 5% – 10% of the tensile strength that it has parallel to the grain. Therefore, tensile stresses in that direction should be avoided or kept to a minimum. This concerns for example curved beams and frame corners in glulam structures. A considerable reduction in tensile strength is caused by defects like fibre disturbances and initial cracks.
Bending strength
The bending strength of wood derives from the combination of its compression strength on the side facing the applied force and its tensile strength in the area facing away from the force.
It describes the wood’s ability to resist bending under application of force without breaking. One differentiates between the modulus of elasticity (MOE) which is used as an expression of stiffness and describes the force under which wood exhibits only elastic deformation, and the modulus of rupture (MOR), the force at which the wood breaks. The MOR is an important factor determining the load-carrying capacity and thus the structural stability of construction components.
Shear strength
Shear strength refers to the ability to withstand forces that cause two adjacent planes of wood (fibres) to slide against each other. Wood is generally stronger and more resistant to shear forces along the grain due to the alignment of wood fibres. The difference to the lower shear strength perpendicular to the grain is significant. In structural design shear strength is an important parameter to consider, particularly for elements such as shear walls, floor or roof panels, and wood connections where shear forces are significant.
Hardness
Hardness is defined as the resistance against penetration by a harder material. This is particularly important for products such as parquet flooring. The correlation between wood density and its hardness is linear. However, the hardness of the end grain surface is higher than on the sides. For measuring wood’s hardness either the Janka test or the Brinell test is applied. The values of these tests cannot be directly compared because even though they look very similar in their set up the methods differ.
Creep
Wood is viscoelastic material that can be deformed through sustained loading. This deformation is called creep and occurs in three phases: In the primary phase the deformation increases until it stabilizes in the secondary phase. If the stress on the wood increases, the tertiary phase is induced which ultimately leads to a break in the structure.
Main factors influencing creep are moisture content, duration of load, temperature, and level of stress.
The creep behaviour also varies between different wood-based materials. As a general rule, creep deformation increases with the decrease in size of the panel components. The relation of creep deformation, i.e., in solid wood : particleboard : fibreboard is at about 1 : 4 : 5
Moisture – The impact of water on wood
Moisture content is defined as the weight of water in wood in relation to the wood mass when it is completely dry (kiln-dry).
As a hygroscopic material, wood fibres absorb water from the surrounding air (adsorption) or release it (desorption) by means of diffusion until an equilibrium is reached. This dynamic causes a change in dimension of the wood because cell walls swell and shrink respectively.
Moisture content also affects other material properties such as the susceptibility to fungal attack (durability), thermal insulation, and strength values. However, the effect on mechanical properties is limited to moisture variations below the fibre saturation point (no free water in the cell lumens).
Shrinking and swelling
The dimensional change of wood is directly linked to its moisture content which is dependent on the surrounding humidity and direct exposure to liquid water. This relation is taken into practical consideration by conditioning products at a level of humidity that is common for their intended purpose. Nonetheless, the possibility of dimensional changes must be considered when installing wood at its final place of service, e.g. by the use of expansion joints in parquet flooring in order to avoid curving.
Generally, swelling of cells is limited to the fibre saturation point where any additional water is present as free water in the cell lumens, which does not cause additional swelling. Most wood species reach their fibre saturation point at 28% – 32% moisture content.
As wood is an anisotropic material the dimensional changes in longitudinal, radial, and tangential direction do not occur uniformly. Wood is the least affected in longitudinal direction while in comparison dimensional change in radial direction is 10 – 20 times higher, change in tangential direction 15-30 times.
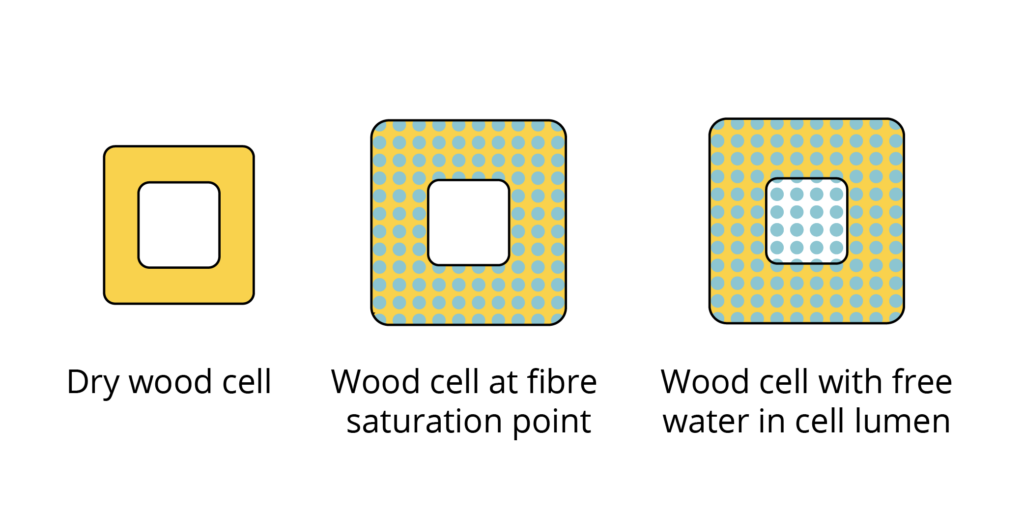
Measuring Moisture content
There are several methods to measure moisture content. The most exact but destructive method is to weigh the material in its moist state and after kiln drying so the mass of water within is calculated and set in relation to the dry weight.
A less destructive and much more practical methods is the electrical resistance measurement. It is the most used technique and handheld devices are available. Two electrodes are inserted into the wood and the resistance of the electrical current in between is measured. A low resistance indicates a high moisture content while a high resistance indicates the opposite. Using this method, it is important to have knowledge of the wood species, the material temperature, and its density as these are properties influencing the result. Most devices come with the possibility to enter the specific data before the measurement is taken.
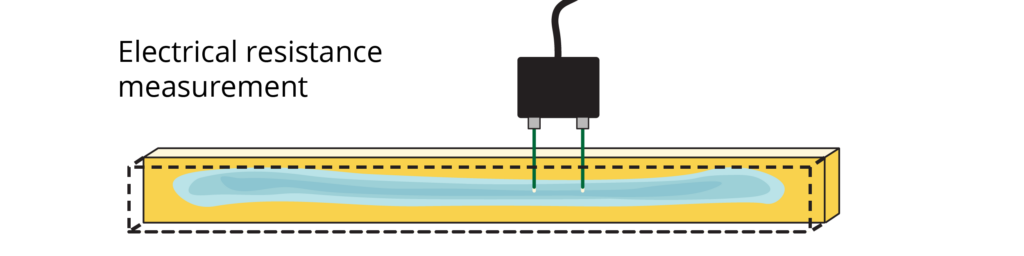
Equilibrium Moisture content
The equilibrium moisture content (EMC) refers to the moisture content at which the wood reaches a balance with the surrounding environment, either by water desorption or adsorption. This is directly linked to the shrinking and swelling of wood. In surroundings with a high relative humidity the EMC will be higher than in surroundings with a lower relative humidity. Due to this relation, it is important to know the intended use of a wood product so that it can be conditioned to the moisture content that it will have during its service life before it is installed. General reference values are available for generic situations such as indoor or outdoor use.
For standardized test purposes wood is conditioned at 20°C and 65% rel. humidity which averages the conditions for indoor use and thus the wood’s moisture content (approx. 12 % regarding most European wood species) in this setting.
Drying of wood
Drying wood leads to a number of advantages. It has a lower weight, and shrinking and swelling is reduced in its final place of use. The resistance against attack by fungi and mold is higher and impregnability increases as well. In addition, dry wood has better strength properties, improved gluability, and the adhesion of paints and varnishes improves, too.
When the tree is freshly cut, there is free water in the lumen and water bound in the cell walls. The moisture content varies greatly across the trunk’s cross section. The heartwood in the center is drier than the surrounding sapwood and there are variations within.
The average moisture content, i.e. in spruce sapwood is at around 80% while the moisture content in spruce heartwood is at around 32% -40%. This affects the initial moisture content of boards and planks produced. Moreover, wood always displays a moisture gradient from the core to the surface that must be considered for the drying process.
The most common method to dry wood is hot-air-drying at up to 100°C. The speed of drying is regulated by the temperature and the water vapor pressure in the drying chamber. Speed regulation is important in order to avoid or minimize the damage that can be caused by a too quick change in moisture content such as cracks and curving of the boards. Independent from the method, good air circulation in between the pieces set into the drying chamber must be ensured.
Durability
Natural durability defines the wood’s ability to resist attack by wood-decaying fungi, mold and possibly insects. When wood is used for exterior applications where exposure to high humidity, liquid water and/ ground contact is expected, wood durability becomes an important property.
Knowledge of the durability under different conditions is obtained partly through experience, partly by carrying out controlled trials under the relevant climate conditions. Natural durability is dependent on the wood species as well as on the differentiation between heartwood and sapwood therein.
There are different methods to ensure and enhance durability, either by construction design or by treatment of the material. In regard to wood-decaying fungi and mold moisture content is always the crucial factor. For colonialization a moisture content of 20% -25% must be present for a longer period of time while for enzymatic degradation by wood-decaying fungi a moisture content above the fibre saturation point is necessary.
Durability classes
Durability classes are defined in standard EN 350:2016 covering wood and wood-based materials.
There are five durability classes (DC 1 – DC 5) regarding the attack by wood-decaying fungi where in class DC 1 the material is very durable and in class DC 5 it is not durable. When this classification is referenced, it only refers to a wood species’ heartwood property. Sapwood is always considered not durable.
Regarding wood-boring beetles with the ability to attack dry wood the only differentiation is made between durable and not durable materials.
The durability in relation to attack by termites is classed as durable, moderately durable, and not durable. The same classification terminology is used for the resistance against attack by marine organisms.
The annex B of EN 350:2016 includes a table giving an overview of a range of wood species and their heartwood durability regarding attack by fungi and wood-boring insects. It puts the heartwood of common softwood species for construction wood such as fir (Abies sp.), spruce (Picea sp.), and pine (Pinus sp.) into durability class 4 (slightly durable) while the pine species Pinus sylvestris, larch wood (Larix sp.), and Douglas fir (Pseudotsuga menziesii)) are listed with a rating of durability class 3-4. With the exception of the last three none of the mentioned species withstand an attack by wood-boring beetles. In contrast to the softwood, oak heartwood i.e. is classified as durable (DC 2) to slightly durable (DC 4), depending on the oak species. Other durable hardwood species are Sweet Chestnut (Castanea sativa) and Robinia (Robinia pseudoacacia) while beech, ash, and birch are not durable.
Fungi: white rot, brown rot, and soft rot
Fungi causing wood decay are sorted into three main groups in relation to the damage pattern that is caused. Brown rot that is common but not limited to softwoods mainly degrades cellulose and hemi-cellulose, leaving behind lignin that results in a brown coloration of the remaining wood at an advanced stage of decay. The wood appears to be broken into small cubes.
White rot is common in but not limited to hardwoods. The fungi degrade all three main wood components (lignin, cellulose, and hemicellulose) either simultaneously or selectively. The degradation of lignin leads to a lighter coloration of the wood. However, the discoloration can be uneven, in stripes or marble-like. At an advanced stage of decay, the wood will be stringy and spongy.
Soft rot can be found in wood with very high moisture content (above 80%) and especially when the wood is in contact with soil. Structures affected by decay appear in brittle cubes as they do when attacked by brown rot because soft rot fungi also mainly decay cellulose and hemicellulose. A very distinct characteristic in soft rot decay are holes in the cell walls caused by growing hyphae therein. As the name indicates, the wood will become rotten-soft under the attack.
(Photo: Viden om Træ, Danish Technological Institute)
Mould
An ideal environment for mould growth is given in the presence of a high relative humidity paired with low air circulation. The attack may cause discoloration of the wood and lead to a decreased (monetary) value. However, it does not affect the strength properties because mould fungi do not decay cell walls. Nonetheless, mould can present a health risk due to spores that are released into the air.
Methods to enhance durability
Enhancing the durability of wood can either be done indirectly by constructive wood protection (i.e. designing wood structures in such a way that protection against run water is maximized) or by additional chemical treatments or modifications of the wood.
Constructive wood protection follows the subsequent principles: The wood should not be directly exposed to precipitation or be installed in locations where moisture accumulates and/or condenses. If the wood does take up moisture it should be ensured that good air circulation enables the wood to dry quickly.
Where wood is exposed, installation should always be at a slight angle of at least 5° to enable run-off. Where screws and nails are used the screw/nail head should form an even surface with the surrounding material so liquid water does not accumulate at these sites. Wood cladding should only be installed at a height where splash water from the ground does not reach.
Drainage around a foundation should lead water away quickly and if wood gets in direct contact with concrete a vapour proof membrane should be installed in between.
Enhancing durability by wood treatment includes several techniques of which the most common are briefly described below.
Wood can be pressure impregnated with biocide to increase its resistance to biological degradation. The target organisms are typically either wood degrading fungi or insects and the wood is typically treated and labelled for use in either above ground situations or for in-ground applications.
Wood can be chemically modified to take up less moisture with the aim of keeping the moisture content below the level necessary for fungal growth and decay. This can achieved e.g. by causing a reaction of the water-binding hydroxyl groups in the wood with non-water-binding /hydrophobic substances.
Wood chemically modified with acetic acid anhydride has been on the market for several years. Another modification technique is to ‘bulk’ the cell wall with polymerization chemical that fills the available voids in the cell wall and permanently swells it. . Thus, the cell wall has a reduced capacity for water uptake. Wood treated by this method has improved dimensional stability and shows increased hardness.
Modification of the wood structure can also be achieved through thermal modification or heat treatment of wood, which breaks down the hemicelluloses that bind a large portion of the water in wood cells. This treatment typically performed at 160°C – 220°C reduces the wood’s mass and therefore also impacts its strengths properties which decrease. Therefore, heat treated wood is not suitable for load-bearing purposes.
Coating of wooden surfaces in outdoor use has the aim of preventing surface-level degradation by UV-radiation and it can also be used as a protective layer against the impact of water when applied correctly. The overall aim dictates whether wood oils, stains or opaque coating / covering paint is used. In general, the wood is always coated once with a primer and only then is followed by the topcoat. Depending on the type of coating the appearance and the maintenance interval varies.
Wood and fire
Wood is, by definition, flammable but it burns predictably at an almost constant rate. When wood burns, a charring layer will form, which protects the underlying, healthy wood. Strength properties do not decrease immediately so that the support and stability in the construction is maintained for a period of time.
Provided that the construction is dense, the low thermal conductivity of wood and wood-based materials minimizes temperature increase on the side facing away from the heat source and thus slows down the spread of the fire. A basis for design calculations is given by classification of materials into fire resistance classes and the use of wood is further controlled by national building regulations.
Ignition and progress
Solid timber is difficult to ignite. For spontaneous combustion without an ignition source the surface temperature must exceed 400°C for a short to medium time frame, and if an ignition source is present the temperature must still exceed 300°C for a specific time. The actual properties in relation to fire depend on the material’s density, species, moisture content, and the ration of the circumference to the cross-section. Fire retardants do not prevent combustion but increase the temperature at which the material combusts. Once wood ignites the fire spreads along the surface at a comparably low speed. The surface area burns vigorously, creating a layer of charcoal that insulates the healthy wood on the inside against the heat on the outside which leads to a delay of further deterioration by fire.
The stability of a structure under fire is retained as longs as the strength values of the remaining, healthy cross-section are not exceeded by the present stresses. During a full-scale fire, evaluating the remaining cross-section of wooden construction materials makes it possible to determine the remaining load capacity and predicting the time until collapse.
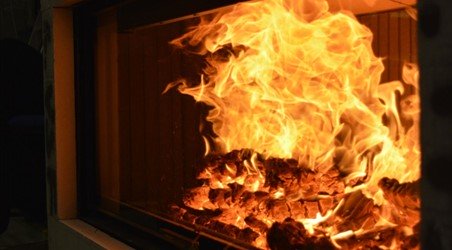
Fire engineering terms and classes
Wood and wood-based materials show a linear correlation of the charring depth and the fire duration. Thus, a constant charring rate is assumed for the calculation of a cross-section’s fire resistance that is expressed in millimeters per minute. It is influenced by the wood species and the density of the product. Wood-based panels exhibit a higher charring rate (ca. 0.9 -1.0 mm/min) than solid timber, glulam and laminated veneer lumber made from softwood or hardwood (0.5 – 0.8 mm/min). The presence of fillets and cracks accelerate the speed of charring. Specifics for calculations are given in EN 1995-1-2 (Eurocode 5 Part 1-2).
Wood and sound / Acoustics
Wood is a light material (low density) compared to concrete and steel. The fact that wood is light can provide many great advantages when it comes to the construction itself. For example, it can lead to simpler foundations. But light materials will more easily be set into oscillations than heavier materials, especially at low frequencies. It is The density of the construction will often ultimately determine how good insulation is achieved in the building.
Physical parameters
Due to wood’s low density in comparison to other materials such as steel or concrete it is more easily set into oscillation, especially at low frequencies. The speed of sound parallel to the fibre ranges approximately between 3.400 m/s and 5.200 m/s, perpendicular to the fibre it spreads slower at 2.400 m/s to 3.200 m/s. In comparison, the speed in air is 340 m/s and in ice and glass between 5000 m/s and 6000 m/s. The speed of sound in wood depends on the type of wood, density, moisture, structure, temperature, and the sound frequency itself.
Sound insulation
When building with wood, two main kinds and sources of sound need to be considered and differentiated between: airborne sound waves, i.e., caused by speech or music, and impact sound where structures are set into vibration, i.e., by walking, and therefore emit secondary sound.
Sound transmission, in general, occurs in two types – direct and flank transmission – and in a building structure it will always be a combination of both. Looking at direct sound transmission, airborne sound will go straight through the separating structure. In this case, and as a rule, the sound transmission decreases with increasing weight of the separating structure. To minimize the travel of airborne sound as much as possible it is also important to ensure airtight transition points between structural elements.
In locations with increased sound insulation requirements (e.g. between different housing units), wood must be either combined with other materials and/or components must be installed in a certain relation to each other to meet the required property. Particular attention must be paid to impact sound in floor separators and flank transmission. This could for example be achieved by a free-standing timber frame wall that is not connected to the load-bearing structure transporting impact sound vibrations and filling with mineral wool reduces air borne sound in addition.
Legal requirements
The spectrum of legal requirements regarding sound insulation varies across European countries. Regulations for housing units – especially multi-story structures – as well as schools and kindergartens are common.
In some countries, regulations also cover further building categories such as office buildings and healthcare facilities. Meeting these sound requirements is usually only mandatory in construction of new building or when an existing structure is renovated due to a change in purpose. However, the exact requirements must be evaluated on a national, regional, or maybe even local level depending on the laws and regulations at the location of the building site.
The possible descriptors used for sound insulation are defined in ISO 717 and the variety given in that standard is reflected in the different implementations across Europe. Also, acoustic classification schemes may be available for housing and other building categories, but they may not be comparable.
If country specific expressions and requirements on sound insulation are converted and expressed in one equivalent value defined as the weighted sound reduction index R’w which describes the airborne sound insulating ability of a building element, the required value ranges between 50-57 dB for multi-story housing and approximately 50-62 dB for terraced housing. Looking at impact sound insulation, the weighted normalised impact sound pressure level L’n,w is set at 65-43 dB and 65-41dB respectively.
Thermal properties
Wood has a low thermal conductivity. Therefore, it feels nice and warm to the touch and it does not contribute to cold bridges in facades, walls etc. Thermal conductivity increases with density and moisture content and is twice as high in direction of the grain than it is perpendicular to it. For common wood species in construction the U-value perpendicular to the gain is between 0.13 and 0.20 W/(m*K).
The specific heat capacity is almost independent from wood species but increases with increasing moisture content. It is at 1300 kJ/(kg*K) for kiln-dry wood. In comparison, the specific heat capacity of concrete is at 900 J/(kg * K).
Volatile organic compounds – Formaldehyde emission
Volatile organic compounds (VOCs) represent a large and chemically diverse group of carbon-based molecules, such as hydrocarbons and other organic molecules, with a high vapor pressure at room temperature. They are emitted into the atmosphere from anthropogenic and biogenic materials and sources.
VOC ‘s are also present in wood, and types and quantities are dependent upon many factors including species, age, and pH value; these emissions differ significantly between hardwoods and softwoods.
Regarding formaldehyde emissions, construction products including wood are tested, and limits are defined within use classes. For wood-based panels the standard EN 13986:2004 applies.