Prefabricated elements
Prefabricated elements are mainly produced from structural timber, I-joist or glulam but can also consist of other EWPs such as cross-laminated timber or laminated veneer lumber.
The wooden frame determines the element’s dimensions in height and width while the thickness of the wood itself varies with the purpose and the required strengths. Dependent on the element’s purpose, the material and number of panel layers is variable. The degree of prefabrication can also come in various levels. Complete modules show the highest level of pre-fabrication.
Prefabricated wall elements
Prefabricated walls can be designed for interior or external use, and they can serve a structural or non-structural purpose. At a minimum, they consist of a frame providing the necessary structural support to the element itself and sheathing to close it.
The frame is often manufactured from cross-laminated timber but can also be composed of glued laminated timber or laminated veneer lumber. The wall cavity underneath the sheathing leaves room to be filled with material for thermal and/or sound insulation as well as other building systems such as electrics and plumbing.
The sheathing itself is commonly made of plywood or OSB that can add to the structural support of the frame and is a base for wall finishes such as panelling or cladding. Dependent on the wall’s purpose, further layers, i.e., a vapour barrier, can be added. Design plans for windows, doors or other openings are integrated into the wall element as the engineered wood products used for the structure are very versatile in their dimensions.
Prefabricated roof elements
Prefabricated roofs from CLT or LVL provide the advantage of being variable and therefore customisable in their shape, size, and design. There are, for example, prefabricated elements available that can span up to 18 meters. Generally, a roof element consists of rafters that are covered on the top and bottom. Dependent on the final place of use and requirements, this covering can, i.e., include a vapour barrier or a breathable membrane. The space between the rafters allows for insulation material to be placed as required and a solid panel covering the top provides the necessary underground for the outermost roof layer.
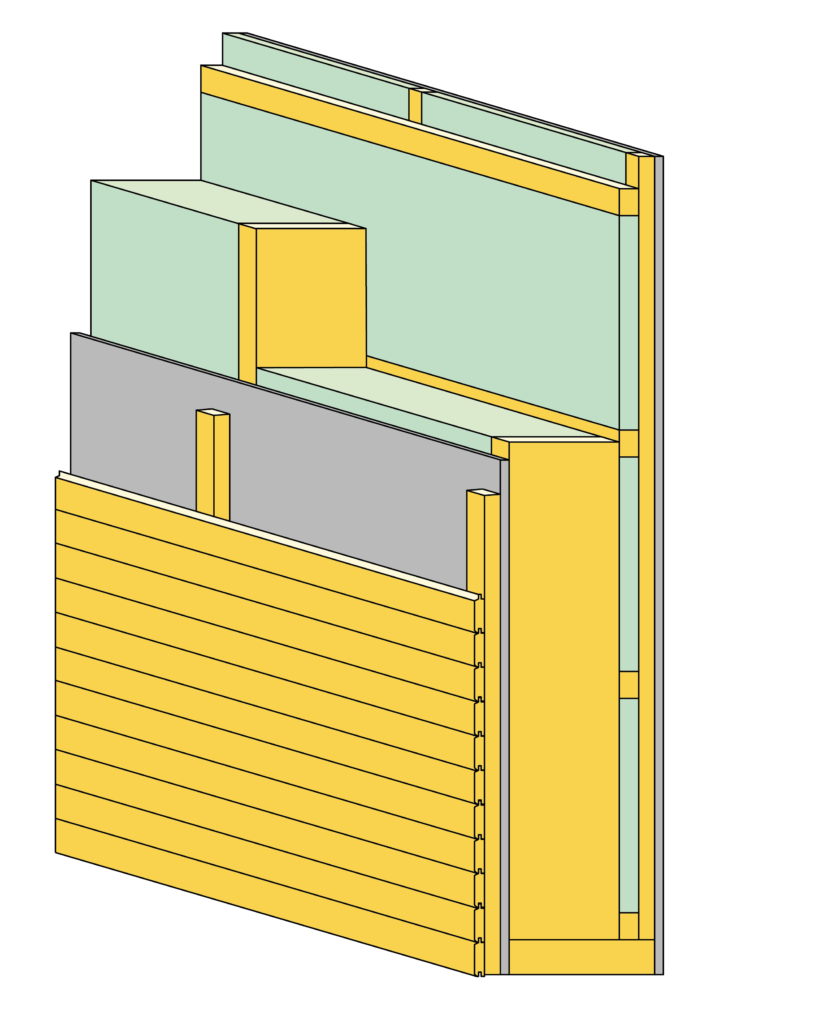
Prefabricated roof elements
Prefabricated roofs from CLT or LVL provide the advantage of being variable and therefore customisable in their shape, size, and design. There are, for example, prefabricated elements available that can span up to 18 meters. Generally, a roof element consists of rafters that are covered on the top and bottom. Dependent on the final place of use and requirements, this covering can, i.e., include a vapour barrier or a breathable membrane. The space between the rafters allows for insulation material to be placed as required and a solid panel covering the top provides the necessary underground for the outermost roof layer.
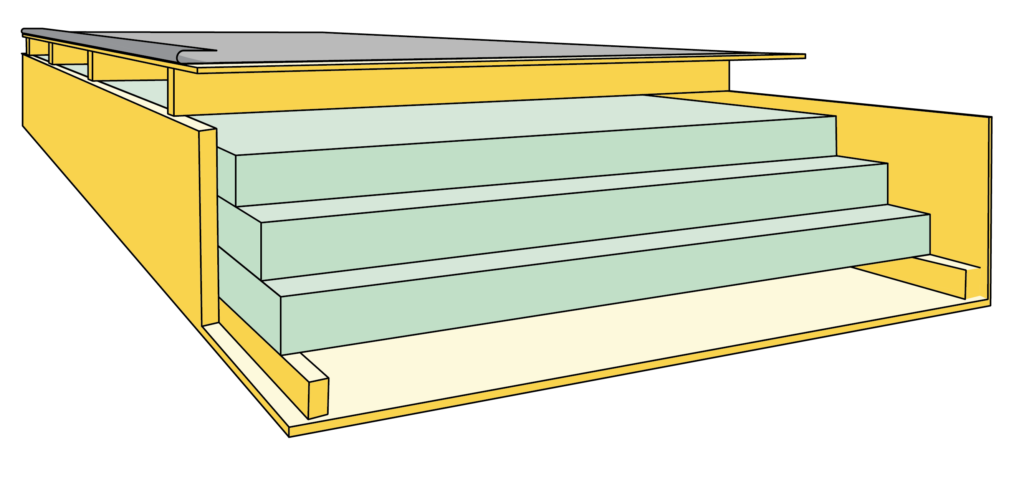
Prefabricated floor elements
Prefabricated floors generally consist of floor joists and bridges while the top is covered by a panel made from LVL, OSB or the like that allows for easy installation of the final flooring surface material. Joists made from LVL or CLT enable the production of long floor elements that can reach a length of approx. up to 15 meters. If the design is open, the joists are visible from the floor below. A closed design where the bottom of the joists is also covered by a panel can be filled with insolation material.
Prefabricated modules
Prefabricated modules take the concept of prefabricated elements one step further and combine these elements to a complete room or unit of a building structure that is delivered as ready to be installed. This can even include the pre-installation of plumbing, electrical, paint, furnishing and appliances. It leads to on-site building completion in an even shorter amount of time and possibly simplifies later add-ons and other changes. Building with prefabricated modules increases in popularity due to its time and cost effectiveness and it is a suitable choice in remote locations or where site access is limited. However, the area must be accessible by truck and a crane and transportation of each module may involve higher costs and risks in comparison to transport of simple prefabricated elements. Solutions for prefabricated module building are offered by a range of companies and vary between the possibility to model the module to your own specifications and having complete house designs “on stock”.
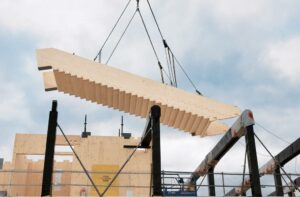
Other types of prefabricated elements
Other prefabricated elements that are available on the market cover but are not limited to applications such as ceilings and interior finishing as well as staircases.
The ceiling (-elements) can consist of two CLT boards that are separated by ribs made from glulam or other structural timber elements or they may be manufactured from finger-jointed solid boards that are interspersed by ribs. In both cases, the top and bottom of the structure is closed, either using further solid finger-jointed boards or panels and the boxed form allows for filling with insulation material to influence the product’s sound and/or thermal insulation properties. The ribs form the side walls and provide additional structural stability by also being glued in the hollow space inside the frame, thus creating smaller compartments or boxes. This results in a high static load-bearing capacity at a low weight and enables column-free building designs due to large spans.
Examples for interior finishings include cladding that improves room acoustic, i.e., in schools and offices, or acoustic cladding that is flexible and withstands impact forces as they occur in sport centres. Prefabricated acoustic panels consist of a base panel carrying the sound absorbing material which is covered by a high-quality wood surface. Depending on the design, these panels can either be laid into or fastened onto a (sub-)structure. The substructure for impact resistant walls is, i.e., made from strips of veneered boards as these are especially suitable for elastic stresses.