Structural timber
Structural timber is lumber that has been strength graded. Structural timber is used for load bearing applications such as joists, roof beams, trusses, rafters, and studs.
Structural timber can be glued together to together e.g. as glue-laminated timber (glulam), laminated veneer lumber (LVL) or cross-laminated timber (CLT) which increases both the load bearing capacity and the application possibilities. Appearance often comes second since the wood is often hidden in the construction. Occasionally, however, there may also be requirements for appearance, such as for visible beams. Non-load-bearing studs have no requirements for strength, but it is still common in many countries to use strength-graded structural timber.
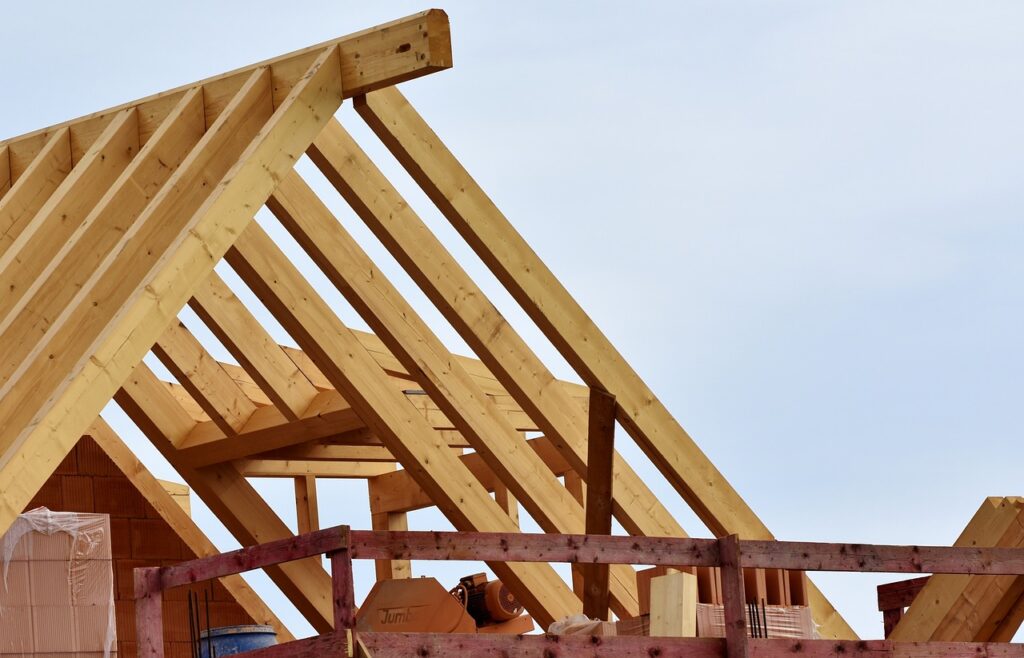
Engineered Wood Products (EWP)
EWP is a broad term for various structural components made of wood. Their production is based on disassembling the natural structure of solid wood by peeling or sawing it into smaller parts that are reassembled afterwards. This method leads to a greater consistency and uniformity in size and strength and the products are versatile in their application. Because the assembly from smaller wooden parts results in increased homogeneity, effects such as shrinking and twisting are reduced.
Glulam
Glulam, or glue-laminated timber, is a structural building material comprising layers of timber, referred to as laminations, glued together. The fibers within each lamination run parallel to the length of the piece, contributing to its high strength class. Glulam exhibits a good load-bearing capacity in proportion to its weight. To optimize material use, laminates in the top and bottom layers – areas subject to maximum stresses – are often of a higher strength class than those in the inner layers.
In contrast to solid wood, glulam has a resilience to smaller defects or knots within individual laminates, minimizing concerns about strength values.
Glulam finds application in different construction scenarios, from smaller buildings and houses where it serves as rafters, beams, posts, lintels, or joists, to larger structures where it is typically used to support large-scale roof structures. Individual glulam members are typically produced in lengths of up to 30 meters but can be produced in longer lengths, in principle only limited by transportation logistics.
Related standards:
EN 14080 (Timber structures. Glued laminated timber and glued solid timber. Requirements.)
Cross-laminated timber (CLT)
CLT is normally used as wall or floor panels. It has three to seven layers of boards or planks, ranging in thickness from 20 to 60 mm. Each layer is placed perpendicularly to the next one. The boards/planks are strength graded, with the strongest grade assigned to top and bottom of the laminations.
CLT has a high loadbearing capacity relative to weight. The low weight is beneficial in transportation, assembly, and foundations.
CLT is manufactured under controlled industrial conditions and in sheltered environments, and it can be produced in dimensions up to 4.8 meters in height and 30 meters in length, with a thickness ranging from 60 to 500 mm. Often, the limiting factor in size is transportation logistics and manufacturing.
The panels can be tailored to the specific building requirements, with precision-cut openings for windows, doors and installations made prior to assembly. CLT can serve as both the fundamental structural element and as the finished interior surface of a building.
Related standards:
EN 16351 (Timber structures. Cross laminated timber. Requirements.)
LVL – Laminated veneer lumber
Laminated veneer lumber (LVL) is made from multiple layers of veneer glued together. It is mostly produced customized for specific projects but comes in standard thicknesses of 24–75 mm and heights ranging from 200–600 mm, with a general ratio limit of 1:8 (thickness/height).
LVL is a very homogeneous material with low deviation in strength and stiffness, which means that these properties can be fully utilized as characteristic values in the structural design of a building project. It has a strength-to-weight ratio twice that of steel.
There are two primary types of LVL:
LVL-P: Fibers run parallel to the length, making it ideal for load-bearing elements like beams, columns, floor joists, and frames.
LVL-C: With 20% of veneers/fibers running perpendicular, it is cross-bonded, enhancing transverse strength and stiffness.
I-joists
I-joists comprising a web and two flanges forming an “I” shape when assembled, are commonly used in both commercial and residential buildings for floor and ceiling construction. They can also function as studs. The flanges are typically made from LVL or finger-jointed solid wood, and the web from plywood, hardboard or OSB-board. I-joists are available in various lengths up to over 20 meters and heights up to about 600 mm.
One advantage of I-joists over solid wood joists lies in their structural strength relative to weight and size. The combination of flanges and web makes them proficient in withstanding both bending and shear forces.
Additionally, I-joists contribute to improved insulation capacity or U-value in a construction. The reduced material usage provides more space for insulation. However, precision is paramount when creating holes in the web for installations, as deviations from correct directives can significantly compromise structural integrity. It’s essential to adhere to established guidelines in this regard. Note that I-joists are more vulnerable to fire compared to solid wood joists.
Wood Based Panels
Wood-based panels play an important role in the construction industry. They covers a diverse selection of boards and panels where wood is the primary component.
Panels can be based on wood in various various forms such as veneer, strands, flakes, chips, particles, or fibres, depending on the intended qualities of the board. Each type of wood-based panel possesses distinct characteristics that make it suitable for specific applications, such as plywood, particleboard, MDF, and OSB.
The manufacturing of wood-based panels plays a significant role in sustainable forestry practices by utilizing wood scraps and pieces, thereby optimizing the efficient utilization of wood resources.
Related standards: EN 13986 (Wood-based panels for use in construction. Characteristics, evaluation of conformity and marking)
Medium Density Fiberboards (MDF) and Particle boards
MDF and particle boards consists of boards that are made from small wood particles and glue, which are mixed with glue and pressed into panels. Particleboards consist of small wood particles of a few millimeters in any direction, whereas MDF consists of individual wood fibers and fiber bundles.
Both products are uniform in nature. The density can be controlled and varied depending on the final quality and intended use of the end-product. Densities typically vary between 500-600 kg/m3 but can be produced within a rangeof 300 to 900 kg/m3.
Especially particle boards, can easily be manufactured from recycled wood and therefore particleboard production fulfills an important role in recycling of wood products. Although they are produced in a range of various qualities, neither MDF or particleboards are high strength products and are typically not used for load bearing applications, except from flooring.
Related standards: EN 622-5 (Fibreboards – Specifications – Part 5: Requirements for dry process boards (MDF)) and EN 312 (Particleboards – Specifications)
OSB
Oriented Strand Boards (OSB) is an engineered wood board made by combining wood flakes/strands with glue, pressed into layers with strands oriented in different directions. While most strands align in the length direction, a central layer typically features perpendicular strands. The strands range from 2.5 to 15 cm in length, providing the board with a textured surface. OSB boards comes in thickness from 5 to 25+ mm and densities from 500 to 750 kg/m3.
OSB offers a rough and varied surface compared to other chipboards with smaller strands measured in millimeters. OSB serves versatile use in construction, e.g. subfloors, underroof installations, ceilings, splice plates, and wall cladding.
Related standards: EN 300 (Oriented Strand Boards (OSB) – Definitions, Classification and Specifications)
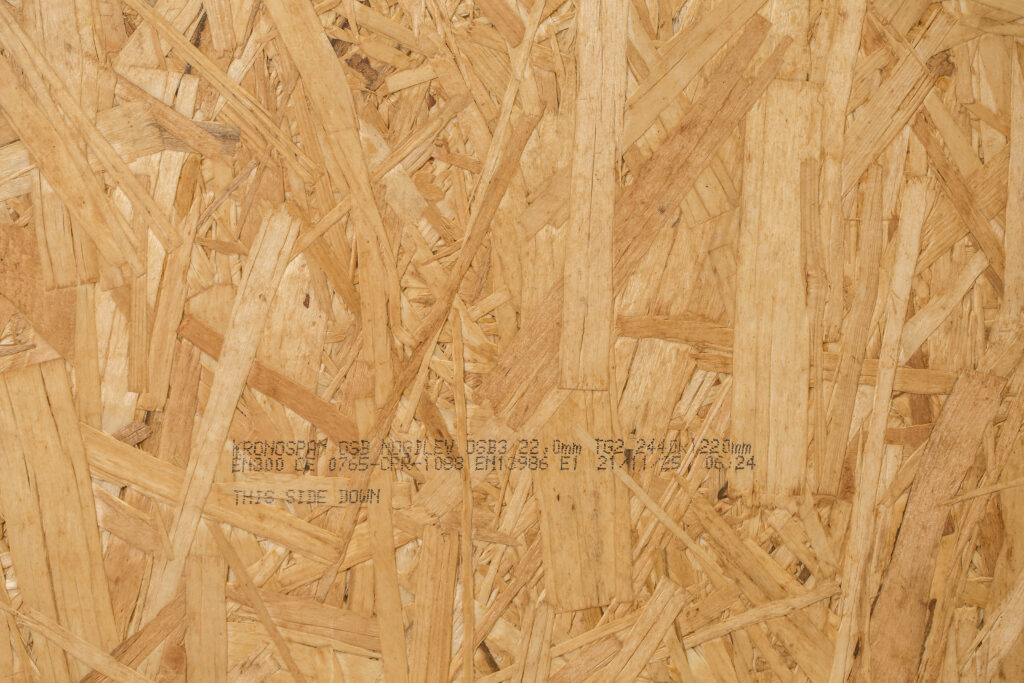
Plywood
Plywood consists of a minimum of three layers of wood veneer bonded together, often with the fibers of each layer perpendicular to the next. Plywood can be produced from a range of species depending on their aesthetics and intended applications. Standard plywood panels typically range from 10 to 30 mm in thickness and width x length 1220 mm × 2440 mm.
Plywood serves diverse purposes in construction such as formwork, subfloors, underroof installations, and wall cladding.
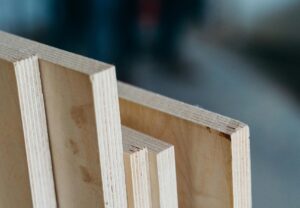